13 Mar Pet najvećih ubojica produktivnosti u industriji PCB-a
Neka rješenja
Put do maksimiziranja produktivnosti tvornice leži u pristupu odozgo prema dolje koji se bavi detaljnim operativnim točkama u prethodnim odjeljcima. Potrebno je poduzeti korake u sljedećim područjima: Priprema podataka Simulacija procesa proizvodnje Priprema proizvodnog procesa Sustavi za izvođenje proizvodnje Za sve ove izazove potrebna su tehnička rješenja. I, što je najvažnije, moraju biti uspostavljeni sustavi izvješćivanja za inženjere, linijske operatere i menadžere proizvodnje koji identificiraju specifične radnje koje je potrebno poduzeti za poboljšanje performansi. Štoviše, informacije moraju biti dovoljno pravovremene kako bi se omogućila poboljšanja prije nego što se izgubi prilika i negdje se pojave novi problemi. Priprema podataka Pozornost na pripremu podataka za unos modela komponente i unos podataka o dizajnu obavezan je prvi korak: Modeliranje komponenti – Proizvođači moraju postaviti točno fizičko modeliranje svih dijelova koje planiraju koristiti na liniji, uključujući kontakte igle za lemljenje spojevi, integrirani s CAD podacima. To bi trebalo uključivati: Dosljedno, neutralno u CAD-biblioteci, modeliranje dijelova kako bi se omogućilo standardizirano DFM i funkcije pripreme procesa nizvodno. Normalizirani pomak komponenti, rotacije i izjave polariteta prema standardu. Svjetska elektronička industrija ima prodaju od 750 milijardi dolara, od čega dvije trećine otpada na montažu PCB-a. Proizvodnju PCB-a karakterizira opsesivni nagon za povećanjem produktivnosti u kontekstu tri značajna pokretača industrije: Kraći životni ciklus proizvoda – Pritisak je da se razviju bolji proizvodi i iznesu na tržište prije nego što to učini konkurencija, uz nižu cijenu, dok se istovremeno razvija proizvod sljedeće generacije. Prije samo pet godina životni ciklus proizvoda mjerio se u godinama; sada se mjere u mjesecima, čime se vrši pritisak na dizajnere i proizvođače da ubrzaju proces prelaska sa faze prototipa na proizvodnju velikih količina. Više složenosti – Proizvođači proizvode složenije dizajne veće gustoće s povećanom minijaturizacijom i sofisticiranijim pločama. Tipični popis materijala (BOM) za sklop PCB-a sada može imati tisuće dijelova ukupno, sastavljenih od stotina jedinstvenih stavki. “Kupljeni” artikli – kondenzatori, otpornici, diode i tako dalje – imat će jedan ili više “alternativnih dijelova” kako bi se omogućila minimalna cijena sastavnice i maksimalna dostupnost dijelova. Složeniji popisi materijala (BOM) stavljaju prednost na povećanu kvalitetu komponenti i bolju sljedivost. Outsourcing brzo raste – Kraći životni ciklus proizvoda i povećana složenost natjerali su OEM-e da prihvate outsourcing, sada najbrže rastući segment industrije PCB-a. Tvrtke Electronics Manufacturing Service (EMS) činile su 21% tržišta u 2004., ali će njihov udio doseći oko 30% do 2008. godine. Sveukupno tržište će za to vrijeme porasti samo 16%. Pružatelji usluga EMS-a nude niže cijene, ubrzanu brzinu izlaska na tržište i bolju izvedbu ispunjavanja narudžbi jer iskorištavaju ogromnu agregiranu kupovnu moć koja proizlazi iz opsluživanja stotina različitih kupaca, te konsolidacijom svojih proizvodnih sredstava i upravljanjem njima kako bi se postigla minimalna jedinična cijena. Pružatelji usluga EMS-a usredotočuju se na svoju temeljnu kompetenciju proizvodnje i nabave komponenti; OEM-ovi se mogu slobodno usredotočiti na dizajn i marketing novih proizvoda. Ovi industrijski trendovi dobro se razumiju i pridonijeli su tome da montaža PCB-a postane jedna od najkonkurentnijih industrija u svijetu. Uz pritisak da se smanje troškovi, dok se istodobno poboljšavaju prinosi i brzina na tržištu, u tijeku je potraga za onim promjenama u tvorničkim operacijama koje mogu poboljšati konkurentnost. Obično je 60-70% uloženog kapitala u dugotrajnu imovinu u operacije montaže PCB-a zaključano u strojevima na montažnim linijama. SMT montaža je posebno kapitalno intenzivna, na primjer, s pojedinačnim linijama koje koštaju više od milijun dolara, a cijena raste. Teško pritisnuti menadžeri proizvodnih pogona pitaju se kako mogu osigurati da njihov uloženi kapital pruži maksimalnu produktivnost i konkurentnost. Odgovor leži ne samo na razini pojedinačnih strojeva, već i na razini cijele linije ili tvornice. Sastavljači PCB-a koriste mnoga mjerenja proizvodnih performansi, od specifičnosti nusproizvoda, vremena ciklusa, brzine otkucaja linije i prinosa prvog prolaza, do mjerila više razine kao što su “trošak konverzije BOM-a” i povrat na uloženi kapital. Koji god se ključni pokazatelji uspješnosti (KPI) koristili, cilj je generirati maksimalan učinak proizvoda prihvatljive kvalitete iz dostupnih montažnih linija, materijala, opreme i ljudskih resursa.
- Dijelovi kaosa
- Neučinkovito postavljanje linije
- Sporije od optimalne brzine otkucaja
- Niske vrhunske performanse stroja
- Kombinacija PCB-a/procesa je podoptimalna
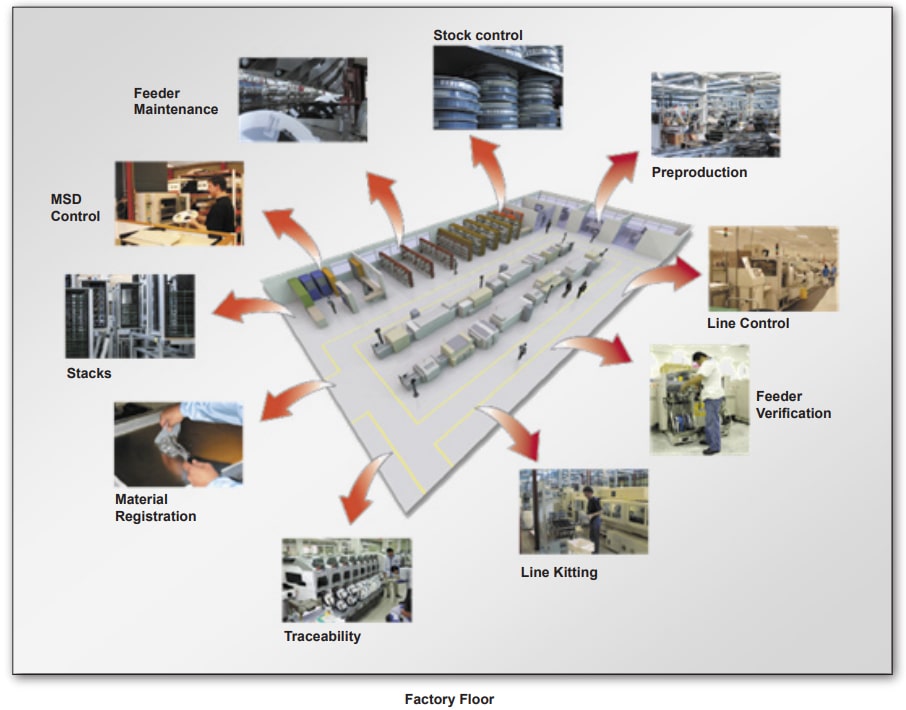
- Dijelovi kaos Prvi problem koji utječe na produktivnost jest to što materijali nisu na pravom mjestu u pravo vrijeme, spremni za upotrebu na montažnim linijama. Mnogi vjeruju da je dovoljno imati potpunu pokrivenost u ERP-u ili glavnom sustavu kontrole zaliha svih sastavnica koje treba sastaviti. Ali kritični čimbenik je imati točne količine dijelova i materijala na raspolaganju i instalirati na strojeve u točno vrijeme kada je to potrebno. Masovna provjera dostupnosti brojeva dijelova sastavnih dijelova ne sprječava neuspjeh proizvodnje zbog nedostupnosti dijelova u tvornici jer:
i. Dijelovi koji su već predani drugim postavkama – Komponente za montažu na PCB obično se rukuju u rasutom stanju – bilo u kolutima koji drže tisuće dijelova ili u hrpama ladica koje drže stotine. Ako su isti dijelovi potrebni istovremeno za dvije proizvodne narudžbe, nijedna linija se ne može ispravno postaviti. Umnožavanje utjecaja ovog problema na stotine kolutova ili ladica komponenti prisutnih na tipičnoj PCB tvornici, povećava rizik nemogućnosti isporučivanja prave količine dijelova linijama za svaku proizvodnu narudžbu, unatoč činjenici da je sveukupno , potrebne ukupne količine dijelova za proizvodne narudžbe odgovaraju ukupnim količinama dijelova u glavnom sustavu kontrole zaliha.
ii. Dostupni dijelovi se ne mogu pronaći – često, u velikim tvornicama, ERP sustavi ne prate vrlo precizno materijale nakon što se puste u pogon. Ključni podaci – u vezi s linijom kojoj su dijelovi dodijeljeni, jesu li postava za koje su predani još u proizvodnji i točna količina dijelova koji su vezani u tim postavkama – često nedostaju. Iako dostupni podaci pokazuju da su dijelovi dostupni za početak proizvodnje, često ih nije moguće pronaći. Nepotrebna kašnjenja rezultiraju početkom proizvodnje dok "ekspeditori" bjesomučno traže materijal koji nedostaje. Jednako tako, i zbog istog nedostatka vidljivosti gdje se dijelovi nalaze, često se dijelovi mogu nepotrebno isporučiti na liniju, kako bi se podržalo postavljanje, kada je zapravo dovoljna količina tih dijelova već napunjena na liniji, ostatak od prethodni proizvodni nalog. Ove netočnosti praćenja rezultiraju nepotrebnim povećanjem cijene zaliha u tvornici. zbog promašaja ili kvara mlaznice prije postavljanja. Uglavnom, to tjera proizvođače PCB-a na precjenjivanje
iii. Dijelovi u karanteni – Drugi čimbenik koji utječe na dostupnost dijelova na stroju za preuzimanje je osjetljivost nekih kategorija komponenti na izloženost normalnim atmosferskim uvjetima u tvornici. Ponekad su komponente pod utjecajem atmosferske vlage nakon raspakiranja iz zatvorenih spremnika i nakon samo nekoliko sati moraju se peći u pećnici kako bi se uklonila vlaga iz tijela komponenti. Prekidi do kojih dovode ciklusi pečenja u pećnici znače da određeni dijelovi prolaze kroz cikluse "dostupnih" i "nedostupnih" za montažu, iako su cijelo vrijeme "na zalihi".
iv. Netočna kontrola zaliha – Dostupnost zaliha dijelova u ERP sustavu često je netočna kao rezultat nezabilježenog otpada. Kada se komponente vrate u skladište nakon uporabe u tvornici, problematično je prikupiti točnu sliku koliko dijelova ostaje na kolutu. Trebaju li voditelji proizvodnje jednostavno uzeti početnu količinu i odbiti broj plasmana definiranih u BOM-u? Vjerojatno ne, jer zanemaruje dijelove izgubljene zbog razine zaliha strojeva, što dovodi do neočekivanih zaliha u tvornici u narednim proizvodnim narudžbama. Ovakva skupa (i neplanirana) obustava proizvodnje stvaraju potrebu za čišćenjem materijala iz linija za naknadne narudžbe i hitnu kupnju dijelova kako bi se ispravili nedostaci. Netočna kontrola zaliha također uzrokuje dugotrajnu i skupu praksu revizije zaliha na cijelom mjestu, kada je proizvodnja u suštini stavljena na čekanje dok se zapisi u ERP sustavu ručno sinkroniziraju sa stvarnošću proizvodnog pogona.
v. razine zaliha, što dovodi do neočekivanih zaliha u tvorničkim pogonima u narednim proizvodnim narudžbama. Ovakva skupa (i neplanirana) obustava proizvodnje stvaraju potrebu za čišćenjem materijala iz linija za naknadne narudžbe i hitnu kupnju dijelova kako bi se ispravili nedostaci. Netočna kontrola zaliha također uzrokuje dugotrajnu i skupu praksu revizije zaliha na cijelom mjestu, kada je proizvodnja u suštini stavljena na čekanje dok se zapisi u ERP sustavu ručno sinkroniziraju sa stvarnošću proizvodnog pogona.
- Neučinkovito postavljanje linije Učinkovita SMT montažna linija ovisi o sposobnosti istovremenog usklađivanja stotina varijabli postavljanja. Ako je bilo koji aspekt postavljanja linije netočan, rezultat je slabe kvalitete. Nekoliko je uobičajenih razloga za sporo postavljanje i otklanjanje pogrešaka:
i. Upute za postavljanje ne odgovaraju programima stroja – U mnogim slučajevima, inženjerski podaci koji pristižu na linije dolaze iz više, nepovezanih tokova podataka. Popis kompleta za svaki stroj vodi se iz BOM-a u ERP sustavu, ali ne uzima u obzir odluke o dijeljenju i balansiranju BOM-a koje su donijeli programeri stroja. CAM sustavi koji se koriste za generiranje strojnih programa često rade iz različite baze podataka od CAM sustava koji se koristi za generiranje tvorničkog puta. A CAM sustavi koji se koriste za programiranje AOI strojeva razlikuju se od sustava koji se koriste za programiranje strojeva za odabir i postavljanje. Fragmentacija tokova podataka može biti opsežna; svaka točka prekida između inženjerskih baza podataka nudi još jednu priliku za generiranje nesinkroniziranih podataka ili uputa za različite dijelove montažnih linija. Sve pogreške u postavljanju moraju se ili eliminirati na izvoru, dizajnom ili otkriti u fazi "prvi-off" i eliminirati uređivanjem uputa za postavljanje dok je linija u prekidu i neproduktivna
ii. Podaci o dijelovima na strojevima nedostaju ili su netočni – Svaki SMT stroj za odabir i postavljanje, AOI stroj i ispitivač u krugu treba biblioteku podataka za opisivanje ključnih karakteristika svake komponente koju treba sastaviti, pregledati ili testirati. Tek kada je biblioteka komponenti stroja popunjena podacima koji opisuju komponente za proizvodni nalog, stroj može obaviti svoj posao. Svaki novi dio utovaren u tvornički pod znači da se knjižnični podaci za taj dio moraju unijeti u strojeve i provjeriti. Nakon kreiranja, podacima se također mora pravilno upravljati jer sve promjene koje se učine mogu potencijalno rezultirati nepotrebnim prekidom rada ako ih ne izvrši kvalificirani operater. Bez kontroliranog i centraliziranog rješenja za upravljanje podacima o komponentama na razini stroja, podaci se moraju pomno unositi u više strojeva, uzrokujući nepotrebno zastoje i visok rizik od nedosljednosti podataka između više strojeva.
iii. Nije postignuta potpuna izvanmrežna postavka – Mnogi proizvođači nisu sposobni za izvanmrežno učitavanje komponenti i provjeru postavljanja. To prisiljava na skidanje i postavljanje linije prije početka proizvodnje, što dovodi do nepotrebnog zastoja. Nema sumnje da se ukupni trošak zaliha ulagača može minimizirati izvođenjem postavljanja on-line, ali se plaća visoka cijena u smislu izgubljene linije i iskorištenosti stroja.
iv. Postavljanje je netočno u fazi prvog ispuštanja – Ako se cjelokupno postavljanje linije ne provjerava paralelno s provjerom inventara na početku, pogreške se moraju otkriti u vrijeme izrade prvog ispuštanja. Ovo je najskuplji način pronalaženja i uklanjanja pogreške u postavljanju, budući da je proteklo vrijeme između stvaranja pogreške i otkrivanja maksimizirano. Pomnožite mogućnosti pogreške/otkrivanja/popravljanja prema broju dovoda, strojeva, programa, a prilika za povećanje vremena otklanjanja pogrešaka prilikom postavljanja postaje jasna, u usporedbi s provjerom svakog aspekta postavljanja dok se provodi. Nakon što je prva faza završena i linija je u punoj proizvodnji, također je od vitalnog značaja da se izbjegnu pogreške kada se novi dijelovi stave na stroj kako bi se napunio iscrpljeni ulagač. U najgorem slučaju, pogrešno postavljeni dijelovi bit će otkriveni nakon sastavljanja cijele serije, u fazi pregleda ili ispitivanja. Takvi popravci imaju maksimalnu cijenu i utječu na ukupnu produktivnost postrojenja.
v. Neuspješno iskorištavanje postojećih postavljanja stroja – Najbolji način da se minimizira vrijeme zastoja u postavljanju je eliminirati potrebu za skidanjem linija i njihovim ponovnim postavljanjem između proizvodnih narudžbi. Zbog složenosti upravljanja velikom raznolikošću komponenti, ulagača, položaja ulagača, količina komponenti i čimbenika koji utječu na optimizirano postavljanje za minimalno vrijeme ciklusa, većina proizvođača uklanja sve dodavače i komponente iz redova između proizvodnih narudžbi. To održava kontrolu, ali dramatično smanjuje produktivnost. Analizom proizvodnih narudžbi unaprijed i identificiranjem grupa proizvoda koje mogu dijeliti istu postavku (ili većinu postava) na montažnoj traci bez žrtvovanja brzine otkucaja do neprihvatljivog stupnja, mogu se postići ogromne uštede u vremenu zastoja. Korištenje tehnika grupiranja proizvoda donosi značajna poboljšanja produktivnosti u operacijama visokog miješanja/niskog do srednjeg volumena gdje su promjene jedan od glavnih faktora zastoja linije.
vidjela. Nemogućnost predviđanja zahtjeva za nadopunjavanjem dijelova – U proizvodnim okruženjima velike količine i niske mješavine, nedostatak unaprijed za točan pristup programiranju linije kao cjeline utemeljen na simulaciji. ii. Strojno programiranje se ne temelji na potpunoj kinematičkoj simulaciji – Ako se simulacija na razini linije i programiranje (balansiranje) odvoje od strojnog programiranja, doći će do sukoba između njih; balansiranje ovisi o točnim informacijama o pojedinačnim vremenima ciklusa, a strojno programiranje može generirati drugačije vrijeme strojnog ciklusa od onoga koje pretpostavlja funkcija balansiranja linije. Ključna je vrlo točna simulacija konfiguracije svakog stroja (ulagači, mlaznice,…) i njegove kinematike gibanja. Bez točnosti u simulaciji vremena ciklusa stroja, ne samo da će patiti performanse pojedinačnih strojeva, već i cjelokupna linija neće biti uravnotežena za optimalan ukupni učinak. vidljivost potrebe za nadopunom dijelova na liniji najvažniji je uzrok zastoja. Najgori slučaj se događa kada su sve komponente u hranilici iscrpljene, ali to je iznenađenje za linijskog operatera (koji mora istovremeno nadzirati stotine hranilica). To tjera konop prema dolje dok se ulagač uklanja, stavlja novi kolut (pod pretpostavkom da je pri ruci) i ulagač se ponovno puni na stroj.
- Brzine otkucaja sporije od optimalnih Nakon što su linije postavljene, proizvodnja se uklopi u svoj ponovljivi ritam, sa sastavljenim PCB-ima koji izlaze s linije fiksnom frekvencijom određenom ravnotežom linije, sposobnostima stroja i razinom optimizacije ugrađenom u proizvod- sami specifični strojni programi. U ovom trenutku na produktivnost utječe na skup, ali nevidljiv način, ako linije nisu programirane da rade pri maksimalnom mogućem otkucaju. To se može dogoditi iz nekoliko razloga: i. Simulacija, cijepanje/balansiranje BOM-a i strojno programiranje ne izvode se na razini cijele linije – Pojedinačni strojevi mogu se programirati na optimalnu razinu, ali ako se zadatku programiranja ne pristupi punom linijom, na temelju kompletne kinematičke simulacije od svih strojeva koji čine liniju, ukupna izvedba pati, prvenstveno uzrokovana neravnotežom radnog opterećenja strojeva. Vrijeme ciklusa, ili brzina otkucaja, linije određuje najsporiji stroj u liniji, naglašavajući potrebu za točnim pristupom koji se temelji na simulaciji programiranju linije kao cjeline.
ii. Strojno programiranje se ne temelji na potpunoj kinematičkoj simulaciji – Ako se simulacija na razini linije i programiranje (balansiranje) odvoje od strojnog programiranja, doći će do sukoba između njih; balansiranje ovisi o točnim informacijama o pojedinačnim vremenima ciklusa, a strojno programiranje može generirati drugačije vrijeme strojnog ciklusa od onoga koje pretpostavlja funkcija balansiranja linije. Ključna je vrlo točna simulacija konfiguracije svakog stroja (ulagači, mlaznice,…) i njegove kinematike gibanja. Bez točnosti u simulaciji vremena ciklusa stroja, ne samo da će patiti performanse pojedinačnih strojeva, već i cjelokupna linija neće biti uravnotežena za optimalan ukupni učinak.
iii. Podaci o dijelovima na razini stroja nisu programirani za optimalnu izvedbu rukovanja – Podaci o dijelovima koje koristi svaki stroj definiraju kako rukovati komponentama: pri kojoj brzini, s kojom mlaznicom, koliko dugo trebaju biti različita vremena zadržavanja, koji se pomaci trebaju primijeniti na mjesto preuzimanja i tako dalje. Dovršavanje prvog pokretanja dovoljno je za provjeru da je proizvod ispravno sastavljen, ali to ne izlaže efekte niske brzine montaže zbog neoptimalnih uputa za rukovanje ugrađenih u biblioteku podataka o dijelovima stroja. Operater će ponekad odlučiti smanjiti brzinu postavljanja komponente kako bi osigurao montažu, često prikrivajući probleme održavanja koje treba riješiti, a uvelike smanjujući ukupnu produktivnost linije. Kao i kod optimizacije samih strojnih programa, bez pristupa detaljnim podacima o izvedbi, ljudima je praktički nemoguće identificirati te učinke; a bez detekcije se ne mogu ispraviti.
- Niske vrhunske performanse strojeva Uz ulaganja u linije koje se kreću do milijuna dolara, jasno je da bi strojeve trebalo održavati tako da rade s maksimalnom produktivnošću tijekom maksimalnog vremena. Međutim, postoje mnogi aspekti stanja stroja koji imaju podmukao učinak na smanjenje ukupne izvedbe.
- Vakuumski tlak u mlaznici – Ako je to izvan specifikacije, uzrokuje ispuštanje komponenti u tranzitu između točke preuzimanja i njihovog položaja na PCB-u.
- Prebacivanje vakuuma na ljepljivu mlaznicu – Ako je vakuumski prekidač ljepljiv, to dovodi do preskakanja mlaznica. Za odabir komponenti iz ulagača bez greške potrebno je pozitivno i brzo prebacivanje vakuumskog dovoda na mlaznice. Isto vrijedi i za plasman; sporo ili neprecizno prebacivanje vakuuma uzrokuje neprecizno podizanje ili postavljanje.
- Istrošene hranilice – To dovodi do visoke stope promašaja. Dodaci komponenti su mehanički uređaji za indeksiranje koji se s vremenom troše. Kako se mehanizam troši uz normalnu uporabu, točnost predstavljanja komponente za preuzimanje opada, što dovodi do neispravnog odabira, što gubi komponente i vrijeme ciklusa. iv. Loše upute za održavanje – SMT linije postavljaju komponente brzinom od nekoliko desetaka ili stotina tisuća dijelova na sat. Ova munjevita brzina stroja otežava promatranje pada performansi. Promašaji se događaju prebrzo da bi bili vidljivi, ali kašnjenje od nekoliko milisekundi na ponavljajućoj funkciji dovodi do neusklađene izvedbe. Bez točne i pravodobne obavijesti o tome gdje su padovi performansi, operateri na liniji i osoblje za održavanje imaju male šanse poduzeti ispravne radnje za povećanje performansi.
- Loše upute za održavanje – SMT linije postavljaju komponente brzinom od nekoliko desetaka ili stotina tisuća dijelova na sat. Ova munjevita brzina stroja otežava promatranje pada performansi. Promašaji se događaju prebrzo da bi bili vidljivi, ali kašnjenje od nekoliko milisekundi na ponavljajućoj funkciji dovodi do neusklađene izvedbe. Bez točne i pravodobne obavijesti o tome gdje su padovi performansi, operateri na liniji i osoblje za održavanje imaju male šanse poduzeti ispravne radnje za povećanje performansi.
- munjevita brzina stroja otežava promatranje pada performansi. Promašaji se događaju prebrzo da bi bili vidljivi, ali kašnjenje od nekoliko milisekundi na ponavljajućoj funkciji dovodi do neusklađene izvedbe. Bez točne i pravodobne obavijesti o tome gdje su padovi performansi, operateri na liniji i osoblje za održavanje imaju male šanse poduzeti ispravne radnje za povećanje performansi.
- Kombinacija PCB-a/procesa je suboptimalna PCB-ovi mogu biti dizajnirani tako da budu prihvatljivi za proces montaže ili neprijateljski prema procesu. Većina PCB-a u konačnici se može sastaviti, ali veći troškovi nego što je potrebno zbog neoptimalnog dizajna, razina prerade i učinkovitosti linije variraju kao rezultat značajki dizajna kao što su:
i. PCB nije pogodan za strojeve ili linije – Fiduciali su skriveni, komponente se sukobljavaju s transporterima, dizajn montažne ploče nije pogodan za optimizaciju. Ograničenja dizajna kao što je distribucija komponenti na ploči ili raznolikost na BOM-u su takva da jedna vrsta stroja ne može postići nisku cijenu postavljanja i to ne postaje vidljivo dok se proizvod ne pokrene na liniji.
ii. Dizajn lemne šablone dovodi do neoptimalnih lemnih spojeva – što rezultira velikom količinom prerade. Primarni cilj montaže je stvaranje pouzdanih lemnih spojeva. Osim dobre kontrole nad procesom lemljenja, kombinacija otvora igle komponente, uzorka jastučića i otvora lemne matrice mora biti optimizirana kako bi se procesu dale najbolje šanse za postizanje spojeva koji su unutar prihvatljivih tolerancija (obično se mjere u desecima loših spojeva, na milijun proizvedenih).
iii. Dizajn PCB-a potiče savijanje i uvijanje – Ploče PCB-a koje se stavljaju na liniju za montažu trebaju biti savršeno ravne, kako bi se izbjeglo „ostajanje” transportera i greške u obradi u strojevima. Dizajniranjem PCB-a s ravnomjernom raspodjelom bakra u svim osovinama, sklonost PCB-a da se savija i uvija tijekom obrade bit će svedena na minimum.
iv. Pad/track uzorci potiču nadgrobne ploče tijekom reflow – S trendom prema manjim pasivnim komponentama čipa, kao što su paketi 0201 koji se sada obrađuju u volumenu, dizajn jastučića i uzoraka staza koji omogućava jednake efekte popuštanja topline na obje strane komponente je sve veće važnosti. Kako komponente postaju svjetlije, učinak površinske napetosti tijekom reflow postaje sve važniji; ako se jedna strana pomakne prije druge, površinska napetost može uzrokovati podizanje suhe strane spoja, uzrokujući efekt "nadgrobnog spomenika".
Neka rješenja
Put do maksimiziranja produktivnosti tvornice leži u pristupu odozgo prema dolje koji se bavi detaljnim operativnim točkama u prethodnim odjeljcima. Potrebno je poduzeti korake u sljedećim područjima: Priprema podataka Simulacija procesa proizvodnje Priprema proizvodnog procesa Sustavi za izvođenje proizvodnje Za sve ove izazove potrebna su tehnička rješenja. I, što je najvažnije, moraju biti uspostavljeni sustavi izvješćivanja za inženjere, linijske operatere i menadžere proizvodnje koji identificiraju specifične radnje koje je potrebno poduzeti za poboljšanje performansi. Štoviše, informacije moraju biti dovoljno pravovremene kako bi se omogućila poboljšanja prije nego što se izgubi prilika i negdje se pojave novi problemi. Priprema podataka Pozornost na pripremu podataka za unos modela komponente i unos podataka o dizajnu obavezan je prvi korak: Modeliranje komponenti – Proizvođači moraju postaviti točno fizičko modeliranje svih dijelova koje planiraju koristiti na liniji, uključujući kontakte igle za lemljenje spojevi, integrirani s CAD podacima. To bi trebalo uključivati: Dosljedno, neutralno u CAD-biblioteci, modeliranje dijelova kako bi se omogućilo standardizirano DFM i funkcije pripreme procesa nizvodno. Normalizirani pomak komponente, rotacije i izjave polariteta prema standardu.
Bez komentara